Вопросы конференции
Сейчас ОАО "Сукно" находится в защитном периоде, и мы будем вводить его в санацию. Предприятие продает ткани, которые используются в том числе нашими силовыми структурами, но не в тех объемах, которые нужны, чтобы работа была эффективной.
Мне не хотелось бы отказываться от идеи создания единого производства, точнее, соответствующего цеха на "Камволе". Это будет абсолютно правильным решением, особенно с экономической точки зрения. На сегодняшний день у ОАО "Сукно" 43 тыс. кв.м площадей с их объемом выпуска чуть более 30 тыс. м. Это нонсенс. На "Камволе" 16 тыс. кв.м площадей. Правда, часть сдается в аренду, но мы считаем, что нужно их зарезервировать и в ближайшем будущем рассмотреть возможность перемещения "Сукна" на "Камволь".
На это есть несколько причин. Во-первых, отходы камвольного производства являются основным сырьем для суконного производства. Во-вторых, у них очень близкая сопряженность по технологическому оборудованию. В-третьих, не надо будет содержать огромный аппарат управления и технологических специалистов.
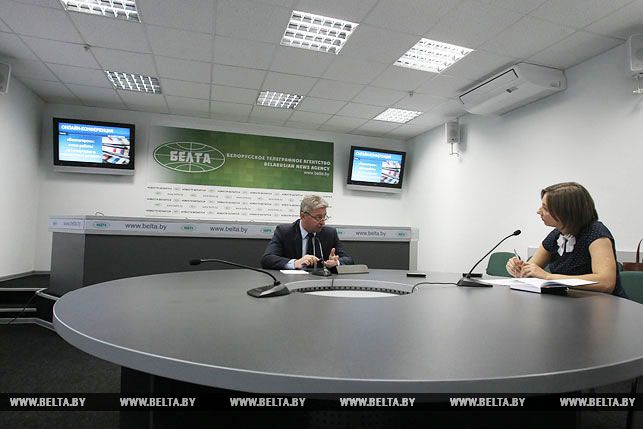
Мы завершили модернизацию "Камволя", сейчас осваиваем абсолютно новый ассортимент. Но в любом случае нужно идти дальше с новыми идеями, потому что весь мир не стоит на месте. В октябре мы должны закончить модернизацию Оршанского льнокомбината, но при этом понимаем, что на первой фабрике слабо идет переработка короткого волокна. Тут тоже срочно нужны идеи, и эти идеи у нас есть.
"Моготекс" проводит очень серьезное техническое перевооружение с привлечением денег из республиканского инвестиционного фонда. Речь идет о сумме в $35 млн. Думаю, что техническое перевооружение полностью завершится в ближайшие два года, потому что уже в этом году часть денег будет получена. За пару лет мы переоснастим весь текстиль, добьемся более высокой производительности и получим абсолютно новые ткани с другими качественными показателями. Будет модернизироваться и ОАО "Лента", но там мы будем привлекать меньше средств. Кроме того, каждое предприятие будет направлять на модернизацию и собственные деньги.
Еще один инвестпроект - "Витебские ковры". Цель - получение полипропиленовых пряж для производства основы под ковры. Это позволит снизить себестоимость готового изделия и не закупать сырье из-за рубежа.
Кроме того, у нас серьезная программа работы с "Белнефтехимом". Мы собираемся все больше использовать химические и синтетические волокна. На "СветлогорскХимволокне" много интересных разработок - филаментные нити, новые виды пряж, полиамиды, полые волокна и нити, которые хорошо пропускают воздух и имеют водоотталкивающий эффект. В будущем возможно производство новой спортивной одежды из полиамидов, которые выпускает "СветлогорскХимволокно". Надеюсь, что "8 Марта" и "Свiтанак" будут сотрудничать в этом плане.
Кроме того, идет техническое перевооружение в ОАО "Могилевхимволокно". Надеюсь, они предоставят нам новые полиэфиры всех видов с антипилинговой обработкой. ОАО "Нафтан" серьезно сотрудничает с ОАО "Полесье", есть ряд предложений по изготовлению волокон с новыми качествами, которые нас очень интересуют.
Так что мы постоянно движемся вперед и в организационном, и в техническом плане, и в использовании новых видов сырья, и, естественно, в получении новых потребительских качеств товаров.
Думаю, за последнее время отношение к легпрому значительно изменилось. Да и позиции на рынке немного меняются. Мы все прекрасно видим, что сегодня "Марко", "Белвест" делают замечательную обувь. Во-первых, на этих предприятиях работаю приглашенные художники - итальянцы, немцы. Во-вторых, это высокое качество, да и цена хорошая - Br60-100 за натуральную классическую обувь. Есть у них и слипоны, и другие молодежные изделия. Что касается домашнего текстиля, то и здесь мы сделали огромный шаг вперед. Какие прекрасные изделия сегодня выпускает Оршанский льнокомбинат, "Моготекс", "Лента". "Полесье" начало выпускать пледы и льносодержащие изделия очень хорошего уровня. Они и по цене доступны, и обладают хорошим внешним видом и качеством. Мало кто умеет подобное делать. Вообще, если взять такой специфический продукт, как лен, то это наше будущее, тем более что это сырье белорусское. И благодаря поддержке государства мы можем смело сказать, что в части переработки льна Беларусь среди первых.
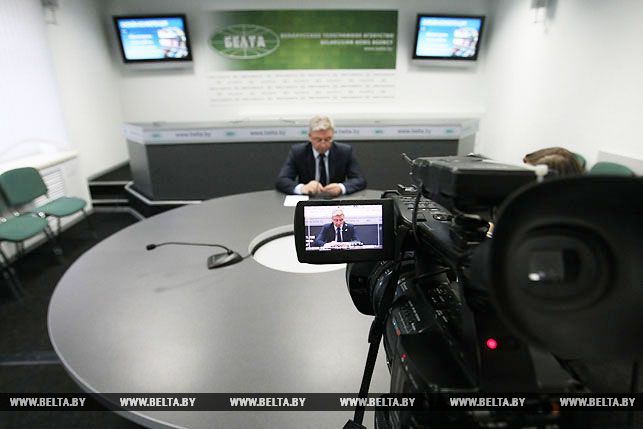
Со временем в холдинг войдут и производители льна, и переработчики. Будем делать так, как это принято в мировой практике. Что-то похожее у нас в стране делается в молочке. Безусловно, тот, кто перерабатывает лен, должен знать, что именно он будет перерабатывать: как сырье росло, в каких условиях и какого качества к нему попадет. Но процесс создания холдинга должен идти спокойно и постепенно, без шоковой терапии.
Сегодня вся добавленная стоимость - это продукция, поэтому экономически самым целесообразным будет присоединить к производителям тканей те предприятия, которые выпускают готовые изделия. Да, у наших предприятий, которые делают ткани, есть свои цеха, но это незначительные объемы переработки. А цель надо ставить более масштабную - максимально перерабатывать собственное сырье, которое производится на наших предприятиях. Варианты присоединения могут быть самыми разными - либо управление акциями, либо просто присоединение, либо создание неких комбинатов. Следующий шаг - надо углублять кооперацию между переработчиками и сырьевыми предприятиями. Это касается всех базовых текстильных предприятий.
Если Орша (Оршанский льнокомбинат. - Прим.БЕЛТА), к примеру, у нас будет ключевым предприятием холдинга, то тут обязательно должны быть собственные швейники. И это должно в ближайшие пару лет обеспечить нам около 50% переработки собственного продукта, т.е. ткани. Сегодня мы перерабатываем чуть больше 15%, в Орше есть свой цех на 200 человек, но это не решает проблему - надо углублять переработку. Сегодня полмира работает с нашими тканями, делают изумительные изделия, а мы - как сырьевой придаток. Кроме того, на переработку мы забираем всего лишь (если взять этот год) 18,9 тыс. т и короткого, и длинного льна, а производится в стране более 40 тыс. т. Надо ставить цель перерабатывать все сырье, которое выпускают наши сельхозпроизводители. А для этого необходимо объединять усилия предприятий, таких как "Гронитекс" и тот же Оршанский льнокомбинат. В какой форме это будет, потом обсудим более детально. У "Гронитекса" серьезная база по приготовлению пряжи, но он может производить только ее. И если выпуск ткани - это производство с малой добавленной стоимостью, то пряжи - еще меньше. Думаю, такая консолидация позволит значительно улучшить и состояние, и перспективы развития этих предприятий.
Кроме того, что производственники объединяются, мы сейчас рассматриваем возможность присоединения к холдингу и наших торговых организаций. Такие консолидированные усилия от сырья до продажи решат ряд проблем: во-первых, отдача от каждого вложенного рубля будет в десятки раз больше, во-вторых, мы будем точно знать, что происходит на рынке и что сегодня актуально для продаж, в третьих, когда ты на рынке доминируешь, то можешь определять, как себя вести и что делать в будущем. Но это не значит, что мы будем монополистами. Беларусь - страна с открытой экономикой, и признать любого из нас монополистом на рынке ЕАЭС - нонсенс. "Моготекс", к примеру, у нас доминирует по специальной одежде на внутреннем рынке, но он производит только около 1% от востребованного объема в России на рынке специальной одежды. Как можно говорить, что он монополист?
Что касается швейных предприятий, то прежде всего планируется кооперация "БелКредо" с "Камволем", потому что они близки по ассортименту и техоснащенности. Для Оршанского льнокомбината ближайший партнер - "Знамя индустриализации", здесь планируется тесное сотрудничество. Думаю, для начала лучший вариант - передача права владения акциями, а в дальнейшем можно рассмотреть возможность присоединения. Также планируется, что Оршанский льнокомбинат будет размещать заказы на пошив одежды в "Свiтанке". А потом мы посмотрим, как углубить кооперацию.
Еще один пример - "Моготекс" и компания "Лона". Все документы подготовлены. Речь идет о присоединении, и это будет абсолютно правильно, потому что они близки по специфике своего производства. Кроме того, "Моготекс" имеет свои цеха и собственное производство.
Барановичское производственное хлопчатобумажное объединение готово к тому, чтобы наладить кооперацию с "Речицким текстилем". Они тоже близки и по производству, и по технологиям.
Абсолютно не боюсь их прихода. Да, Zara - бренд, это мировая сеть, наверное, с самым высоким товарооборотом. Но зайдите в Zara и посмотрите составы тканей, с которыми они работают. Я не увидел ни одного костюма, в котором 100% натуральных волокон (хлопок, шерсть, лен). Там все основано на синтетических тканях. Даже не на химических волокнах - вискозе, а на полиэфирах. И вот здесь мы будем выигрывать, потому что не так оголтело используем химические ткани, хотя, наверное, и нам придется увеличивать их производство из-за низкой стоимости конечного продукта.
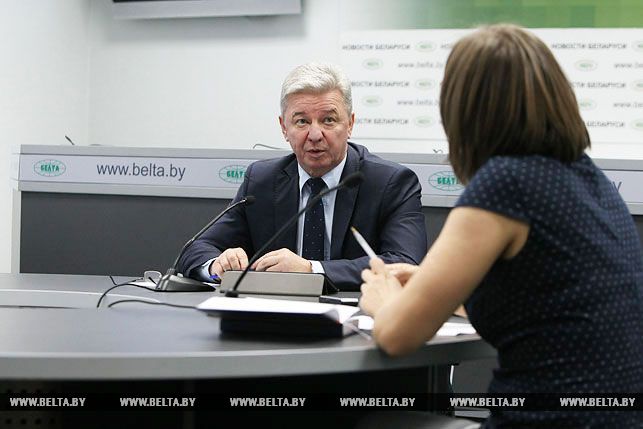
Абсолютно согласен: мы научились производить, у нас есть понимание, как это сделать, а вот продавать, к сожалению, не умеем. И это наша беда, мы пытаемся с ней бороться. На специализированной выставке, которая пройдет осенью, будем приглашать специалистов по продажам, которые детально проконсультируют, поделятся опытом. Мы не умеем показать свой товар лицом. Зачастую наша продукция, которая выигрывает во всех отношениях - по цене, качеству, функциональности, не представлена, как следует.
Что начальники от образования, что мы не собираемся навязывать через колено единую форму. У нас есть одежда делового стиля, ее носят в школах и гимназиях. Но многие естественным образом начали приходить к тому, что выбирают единый стиль для учреждения образования. И в этом мы абсолютно их поддерживаем.
На опыте нашей подшефной школы №101 скажу, что поначалу было непонимание. Но три года назад мы одели младшие классы, потом дошли до 8 класса, учителей. Теперь понимаем, что скоро до 11 класса дойдем.
Предприятия легкой промышленности предлагают родителями около 700 моделей. Они есть в интернете - как на сайтах предприятий, так и на сайте "Беллегпрома". Мы готовы принять заявку любого учреждения образования на изготовление этих изделий. Просто надо четко определиться по времени и по возможностям наших предприятий.
Вообще думаю, что единый стиль одежды для учреждения образования - это правильно. И мы к этому придем, просто нужно чуть-чуть подождать. Отличия в школе должны быть по уровню знаний, а никак не в одежде. Тем более что единый деловой стиль не ущемляет интересов ни родителей, ни детей, ни преподавателей.
Конечно, всегда найдутся те, кто не захочет придерживаться единого стиля. Но приоритетное право принять решение остается за педагогическим и попечительскими советами школы. Родители и учителя должны договориться.
В этом году мы выпустили более 1,5 млн изделий делового стиля для детей, около 500 тыс. пар обуви. И производство пока не останавливаем - если торговле будет нужно, поставим еще.
Директор школы должен позвонить на предприятие, модели которого понравились, и предложить заказ на определенное количество изделий. И договориться по срокам. В этом году мне звонили некоторые директора и просили поторопить предприятия с выполнением заказа. Конечно, я просил максимально ускориться, шли навстречу. А вообще глобальных проблем не было и, думаю, не будет. Потому что все предприятия заинтересованы поучаствовать - это хорошие заказы.
Чем раньше, тем лучше. Надо понимать, что технологический процесс производства на швейном предприятии из наработанных моделей тканей составляет максимум 60 дней. Если с нуля нужно произвести и пряжу, и ткань, и изделие, то 90 дней. По сути, все как в модной индустрии: обычно весной делается заявка на осень, чтобы процесс производства с нуля привел к торговле и торговля продала. Если к началу лета будет заказано, то к сентябрю мы изготовим то, что надо.