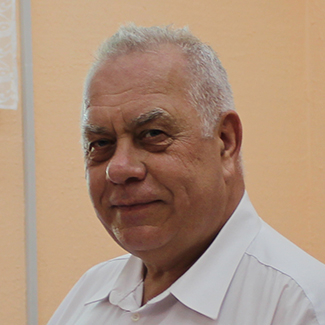
Сегодня промышленное предприятие имеет будущее, если у него есть своя сильная конструкторская школа. Ведь собственные инновационные технологии не только значительно повышают конкурентоспособность компании, но и являются мостом в будущее. МПЗ - один из немногих подшипниковых предприятий бывшего Советского Союза сохранил конструкторское направление. Как отвечают белорусские специалисты на вызовы времени, о наработках предприятия, особенностях профессии, предстоящих планах корреспонденту БЕЛТА рассказал главный конструктор Минского подшипникового завода Анатолий Бахуревич.
- Что представляет конструкторское направление в структуре МПЗ?
- В советское время функционировало порядка 30 подшипниковых заводов. Каждый из них специализировался на какой-то определенной конструктивной группе подшипников. Специализацией нашего предприятия было производство и выпуск роликовых, радиальных, сферических двухрядных подшипников нормального класса точности для применения в горнодобывающей, металлургической, энергетической отраслях, крупного машиностроения, нефтегазовой промышленности. И конструкторский отдел бюро ГПЗ-11 (так тогда назывался наш завод) занимал лидирующие позиции в союзной подшипниковой отрасли.
После распада СССР наша конструкторская служба сохранила все традиции и компетенции, предлагая разработки топового уровня. В задачи нашего отдела входят разработка и проектирование подшипников, удовлетворяющих требования потребителей, а также подготовка нормативно-правовых актов, ГОСТов, технических условий, по которым наша продукция изготавливается.
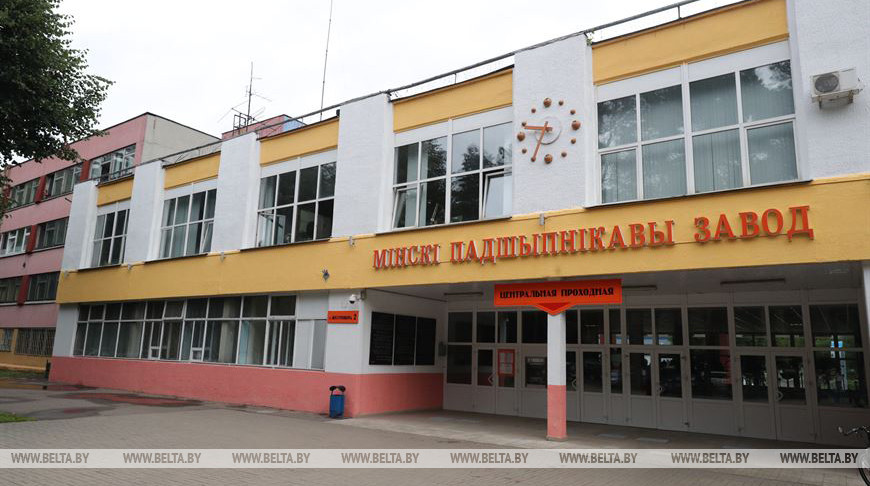
Кроме этого, в наши функции входит участие в составлении годовых планов выпуска и графиков освоения новых типов продукции, испытание и внедрение в производство новых и модернизированных конструкций подшипников. Помимо этого, мы проводим стендовые испытания изделий, проводим исследования продукции предприятий-конкурентов, выполняем работы по сертификации, поддержке товарных знаков. В целом, работы много, но мы стараемся делать ее качественно, в срок и на самом высоком уровне.
- Про конструкторов говорят: встречают по одежке, провожают по чертежу. Каков кадровый потенциал?
- Численность отдела главного конструктора составляет 17 человек. В конструкторском бюро трудятся много молодых специалистов. Они - интеллектуальное будущее нашего завода. Мы возлагаем большие надежды на молодежь, и нам есть чему ее научить.
В наш отдел также входят лаборатория испытаний, конструкторское бюро стандартизации с техническим архивом и множительным центром, а также бюро новой техники, включая научно-техническую библиотеку.
- Ваш многолетний конструкторский опыт включает в себя советскую школу конструирования и современную. В чем их общность и различие?
- Говоря о советской школе, я вспоминаю кульман, счетную японскую машинку Canon, которая была одна на все конструкторское бюро. Однако методика проектирования подшипника в то время была с достаточно полным объемом расчетов, с использованием различных расчетных коэффициентов, определяющих прочностные, технические и эксплуатационные характеристики подшипников.
Современная же школа включает в себя уточненную методику расчета с набором обработки данных на электронных вычислительных машинах, она учитывает явления, которые происходят в подшипнике в процессе его эксплуатации, а также напряжения рабочих поверхностей деталей в зоне контакта подшипника. В целом, лучше охватывает те моменты, которые влияют на долговечность. Можно сказать, что в этом плане современная школа более продвинутая.
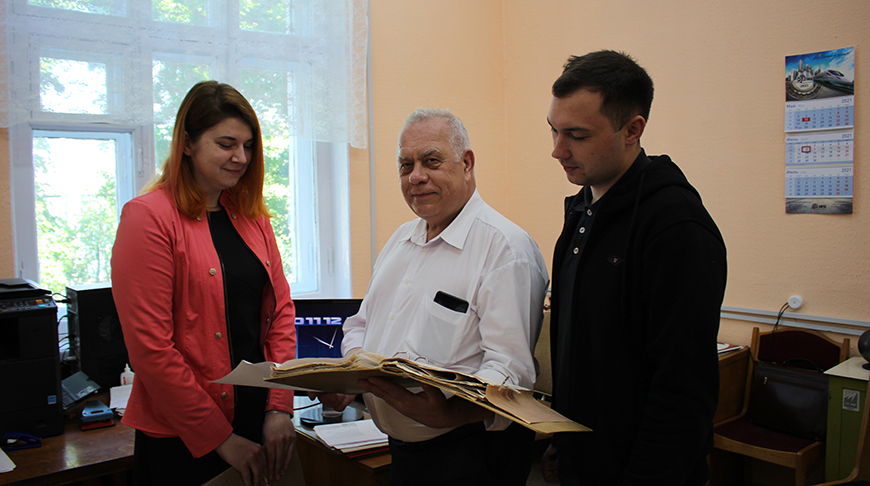
Кроме того, конструкторские разработки советского периода были более металлоемкие, сейчас же идет тенденция к снижению веса подшипника, уменьшению его поперечного сечения. И требований к нему сегодня предъявляется гораздо больше. Все стали считать свои деньги, поэтому практически каждый потребитель ввел входной контроль подшипников перед его установкой в узел. Он включает обязательную визуальную проверку внешнего вида, измерение твердости деталей переносным прибором, измерение радиального зазора и так далее.
При конструировании и производстве своих подшипников мы в том числе ориентируемся и на опыт передовых западных компаний. Качество изготовления, технические и эксплуатационные характеристики нашей продукции сопоставимы с подшипниками, изготавливаемыми топовыми зарубежными производителями. И поэтому конкурировать удается довольно-таки успешно.
- Расскажите про свой первый проект? И что значит для вас процесс конструирования?
- Моим первым серьезным проектом был роликовый игольчатый подшипник со стальным М-образным сепаратором, который мы производили для Тульского машиностроительного завода и Ковровского завода имени Дегтярева. Он использовался для комплектации поршневой группы двигателей мотоциклов и мотороллеров. Однако самым значимым проектом была организация и освоение импортозамещающего производства роликовых конических подшипников для использования в ступицах колес, редукторе главной передачи и дифференциале заднего моста автомобилей МАЗ, а также для применения в самосвалах БЕЛАЗ, тракторах МТЗ, троллейбусах и так далее.
Я много лет работаю конструктором, за это время было спроектировано и запущено в производство немало проектов. И я отслеживаю их в течение всего жизненного цикла до конечного процесса эксплуатации.
- Тяжело ли МПЗ конкурировать с ведущими мировыми компаниями в сфере конструкторских разработок?
- Скажу откровенно, конкуренция дается непросто, однако у нас многое получается. Некоторым передовым компаниям мы уже наступаем на пятки и производим продукцию, которую они еще не делают. В частности, выпускаем закрытые подшипники в открытых габаритах. У SKF пока такого нет.
В принципе, мы довольно гибкие, всегда идем навстречу потребителю. Например, вместо серийного подшипника можем изготовить специальный.
- Расскажите о вызовах, с которыми сегодня приходится сталкиваться заводским конструкторам и как они отвечают на них?
- Каждая компания стремится иметь свои импортозамещающие производства, поэтому нашу продукцию начинают осваивать и другие предприятия. В итоге становится жестче конкуренция. Однако мы не стоим на месте, всегда стараемся найти выход. К примеру, благодаря анкетированию потребителей, мы узнаем, какие недостатки есть у подшипников. Ведь нельзя поставить универсальный, классический подшипник в любой узел, под каждый необходимы специальные условия эксплуатации. В связи с этим мы стали делать специальные подшипники под конкретный случай. И тем самым нам удается уходить от конкурентов.
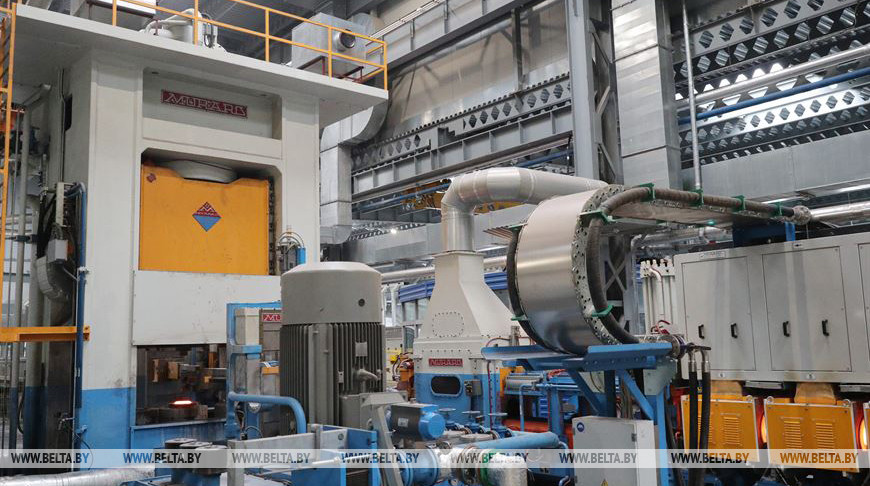
- Какие разработки МПЗ за последние годы вы считаете наиболее значимыми?
- Как я уже сказал, для меня все подшипники важны и дороги - они для меня как дети. Из самых значимых могу назвать крупногабаритный шарнирный подшипник для БЕЛАЗа (ШСЛ150), для внутреннего аккумулятора МАЗа, нестандартный подшипник для поддержки цепи для Белорусского металлургического завода. Сейчас, по просьбе БМЗ, мы его модернизируем, сейчас он находится на стадии испытаний.
Также мы освоили подшипники из стали, изготовленной по европейским стандартам.
Особо хочу отметить подшипники виброустойчивого исполнения (они применяются в узлах, где изначально технологически заложена вибрация), а также подшипники для реверсивного движения (направление вращения у них происходит то в одну, то в другую сторону). Наши конкуренты, если и делают что-то подобное, то на значительно худшем уровне. Мы же являемся в этом плане лидером, у нас более 50 типов данных подшипников. Сюда же можно отнести закрытые подшипники с двухсторонним резиновым армированным уплотнением и заложенной туда смазкой для работы в загрязненных условиях и в агрессивных средах, крупногабаритные шарнирные подшипники с одним или двумя разломами (в частности, такие делаем для БЕЛАЗа и других отечественных флагманов), шариковые многорядные подшипники, радиально-упорные для нефтегазовой промышленности.
Еще наиболее значимые наши разработки - это подшипники двойного назначения: для российского военно-промышленного комплекса (корпорации "МИГ" и "Сухой") и атомных электростанций. Кроме того, мы сконструировали подшипники для подводных лодок.
В прошлом году МПЗ вышел на новый премиальный рынок Евросоюза - Германию. В сентябре мы выиграли тендер на поставку компании Ventprom Deutschland GmbH подшипников, которые применяются в вентиляторах, устанавливаемых в шахты по добыче угля. В начале этого года мы уже отгрузили их немецкой стороне. Сейчас они проходят испытания в Дрездене.
- Велик ли разрыв между конструированием изделия и внедрением его в производство? На сколько типов подшипников разработана документация и сколько их находится сегодня в массовом производстве?
- От поступления заявки до разработки конструкторско-технологической документации, изготовления оснастки, измерительного инструмента необходимо порядка шести месяцев. У МПЗ имеется конструкторская документация на более чем 1,5 тыс. типов подшипников. В любой момент мы можем запустить их в производство. В среднем изготавливаем около 1 тыс. подшипников. Некоторые мы делаем раз в месяц, некоторые раз в квартал, как поступит заказ. Сейчас в производстве около 800 типов подшипников.
- Легко ли внедрять инновационные разработки в работу завода?
- При наличии технологий, оборудования - это делать абсолютно нетрудно. В конце минувшего года МПЗ завершил масштабное техническое перевооружение, поэтому мы, можно сказать, в техническом всеоружии.
- На МПЗ конструкторы за десятилетия разработали тысячи видов подшипников. А это же кладезь продажи технологий…
- И конструкторы, и руководство завода готовы к созданию совместных производств, где были бы востребованы и задействованы по всем параметрам наши технологии. МПЗ очень перспективное предприятие, которое нуждается в инвестициях. А предложить технологии производства мы можем самые современные. Не зря в свое время шведская компания SKF хотела купить у нас цех по производству сферических роликоподшипников.
- Недавно МПЗ приступил к разработке опытных образцов шариковых подшипников для аэрокосмической отрасли Китая. Расскажите о них подробнее?
- Да, это действительно так. Китайцы к нам обратились с данным заказом. Мы заключили с ними договор. Пока все пройденные этапы оказались успешными. Положительный результат испытаний позволит нам выйти на рынок КНР.
- Расскажите про такое перспективное направление, как создание подшипников для железнодорожного транспорта?
- В свое время МПЗ был основным поставщиком буксов вагонов для железной дороги. Поставки достигали 200 тыс. единиц в год. Однако с течением времени проектировщики буксов перешли на другую группу подшипников. А в СССР, как я уже упоминал в начале нашей беседы, у заводов была определенная довольно узкая специализация, поэтому разработку и производство новых подшипников передали другим предприятиям - Харьковскому подшипниковому заводу №8 (сейчас - "Харп") и Степногорскому заводу №16 (АО "ЕПК-Степногорск").
В настоящее время у нас есть очень большое желание вернуть позиции поставщика подшипников для железнодорожной отрасли. В этом плане все конструкторские работы уже проведены. У нас готовы чертежи, технологии, разработана документация для подшипников, которые могут использоваться на железных дорогах Турции, Польши. Также рассматриваем возможности поставок такой продукции в страны Азии и Африки.
Сегодня у нас имеется порядка 40 типов размеров ж/д подшипников. Это довольно большой потенциал, но нужны существенные инвестиции на покупку специальных станков, оборудования для термообработки внутреннего кольца, установки для изготовления пластмассового сепаратора, суперфинишного оборудования.
- Минский подшипниковый завод начал активно возвращаться на крупнейшие конвейеры Беларуси и России. Как конструкторы планируют поддержать этот тренд?
- МПЗ разработал программу импортозамещения на 2021 год. В нее включены 42 типа размеров новых импортозамещающих подшипников. За первый квартал 11 типов размеров подшипников уже изготовлены и реализованы. Мы сотрудничаем в этом направлении с такими отечественными флагманами, как БЕЛАЗ, МТЗ, МАЗ, МЗКТ, "Белкард" (30 тыс. подшипников поставляется ежемесячно), "Бобруйскагромаш" (20 тыс.).
- Какие еще проекты являются приоритетными для заводских конструкторов?
- Наш приоритет - крупногабаритные шарнирные подшипники, шариковые многорядные для нефтегазовой промышленности, подшипники для авиаотрасли (для СУ-57), также набирают популярность подшипники из стали (100-хром-6) по европейским стандартам изготовления.
- Мы живем во времена стремительного развития технологий. Куда, на ваш взгляд, придет конструкторская мысль к середине столетия?
- В ближайшей и долгосрочной перспективе промышленность, думаю, перейдет на мехатронные подшипники. Это подшипниковые узлы со встроенными в них датчиками, которые будут определять ресурс работоспособности подшипника в реальном времени. Например, в буксах железнодорожного транспорта стоит подшипниковый узел со своими корпусами, встроенными уплотнениями, и в него вмонтирован датчик, который у машиниста на экране будет показывать состояние этого подшипника, сколько он еще сможет проработать.
Будет развиваться изготовление подшипников со специальными покрытиями, укрепляющими их поверхностный слой, керамических - для газотурбинных, реактивных двигателей.
Впрочем, стремительное развитие технологий готово в будущем привнести самые неожиданные конструкторские и технологические решения.
БЕЛТА.-0-